Ceramics
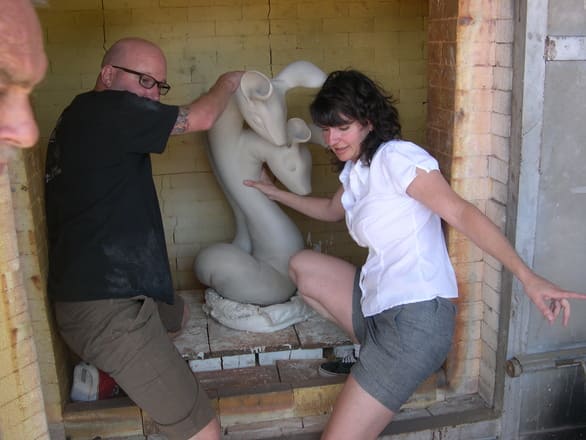
The focus of the ceramics program is to challenge students intellectually by providing an opportunity for an art-making experience with an emphasis on contemporary sculpture. The goal is to encourage and guide the evolution of the each student's aesthetic sensibilities as they strive to understand and define their place in the world.
Equipment
- Skutt electric kilns (computerized with a 7 cubic-foot chamber)
- Skutt electric test kiln (with a 0.8 cubic-foot chamber)
- Fire Master electric kiln (with a 7 cubic-foot chamber)
- Fire Master electric kiln (with a 6.5 cubic-foot chamber)
- West Coast gas kiln (with a 14 cubic-foot chamber)
- Alpine gas kiln (with a 9 cubic-foot chamber)
- Raku kiln (with a 7 cubic-foot chamber)
- Walker pug mills
- Bluebird clay mixer
- Slipmaster slip mixer
- Studio Star slip casting table
Classroom
The classroom is the main activity center of the facility and is usually buzzing with students working on their projects. It is broken up into two connecting rooms, one for the beginning ceramics course and the other dedicated to the intermediate/advance students. This allows students full access at any time without interrupting classes in session. Cabinetry lines the walls allowing most students their own personal cabinet to keep their work and tools. There are wedging tables and large work tables. These rooms also contain four electric wheels, one slab roller, as well as an extruder.
Clay room
This room includes two pug mills, one commercial slip-casting table, one slip-casting mixer and a small countertop to work on while slip casting. The clay mixer is just outside the door for easy access.
Kiln room
The kiln room contains three computerized Skutt kilns, one large Fire Master kiln and one small Skutt kiln for testing glazes and clay bodies. Shelves line one wall of this room for storage of greenware that is ready to fire.
Patio
The large patio space is partially hooded and vented. There are two fully functioning gas kilns, as well as a raku kiln and an additional electric kiln. The West Coast gas kiln easily accommodates large-scale work that does not fit into "conventional" kilns as its interior dimensions are (L)6.25'x (W)3'x(H)5'. Shelving lines the wall for stockpiling necessary chemicals. There are work tables in this area for the production of plaster molds. There are no salt, soda, nor wood firing kilns.